Quality Management System & Certifications
Our Commitment to Global Quality Standards
ISO Certifications
Our manufacturing facilities are certified to ISO 9001:2015 (Quality Management System) and ISO 14001:2015 (Environmental Management System), ensuring consistency, sustainability, and process control throughout every stage of production.
Industry-Specific Certifications
Depending on customer needs and export markets, our products comply with various international standards, including:
RoHS/REACH compliance
MIL-C-675C durability standards
Other application-specific requirements upon request
Factory Audits
We have passed BSCI audits and third-party inspections by leading international clients, demonstrating our adherence to global manufacturing and ethical standards.
Quality Policy
We are committed to delivering high-quality optical solutions that meet or exceed customer expectations through continuous improvement, rigorous quality control, and a zero-defect mindset.
Material & Component Quality Control
Precision Starts at the Source
Supplier Management
We work exclusively with globally recognized suppliers. All vendors must meet strict qualification standards and undergo regular performance reviews and audits.
Incoming Quality Control (IQC)
Every batch of optical glass, coatings, and housing components is subject to thorough incoming inspection for:
Dimensional Accuracy
Optical Clarity
Surface Quality
Compliance with RoHS/REACH Directives
Traceability
All critical materials are tracked using batch numbers or serial IDs, enabling full traceability throughout production and post-sale service.
Material & Component Quality Control
Precision Starts at the Source
Outgoing Quality Control (OQC)
Each product undergoes a comprehensive final inspection before shipment. All pass/fail results are documented and archived.
Visual Inspection
100% visual inspection under controlled lighting conditions for defects, labeling, and packaging.
Test Reports
Inspection and testing reports are available upon request for each shipment or production batch.
Functional Testing
Core product performance is tested, including:
• Light transmission
• Anti-reflective coating effectiveness
• Polarization accuracy (for CPL filters)
• IR/UV cut-off precision
• Optical flatness and parallelism
• Scratch and dig validation (per MIL-PRF-13830B)
• Coating durability and environmental resistance
Environmental & Reliability Testing
• Thermal cycling: -40°C to +85°C
• Humidity test: 85% RH at 65°C for 96 hours
• Salt spray test: for metal parts and coatings
• Drop and vibration tests: simulating transport and end-use conditions
Packaging & Logistics Quality Assurance
Safe Transport from Factory to Field
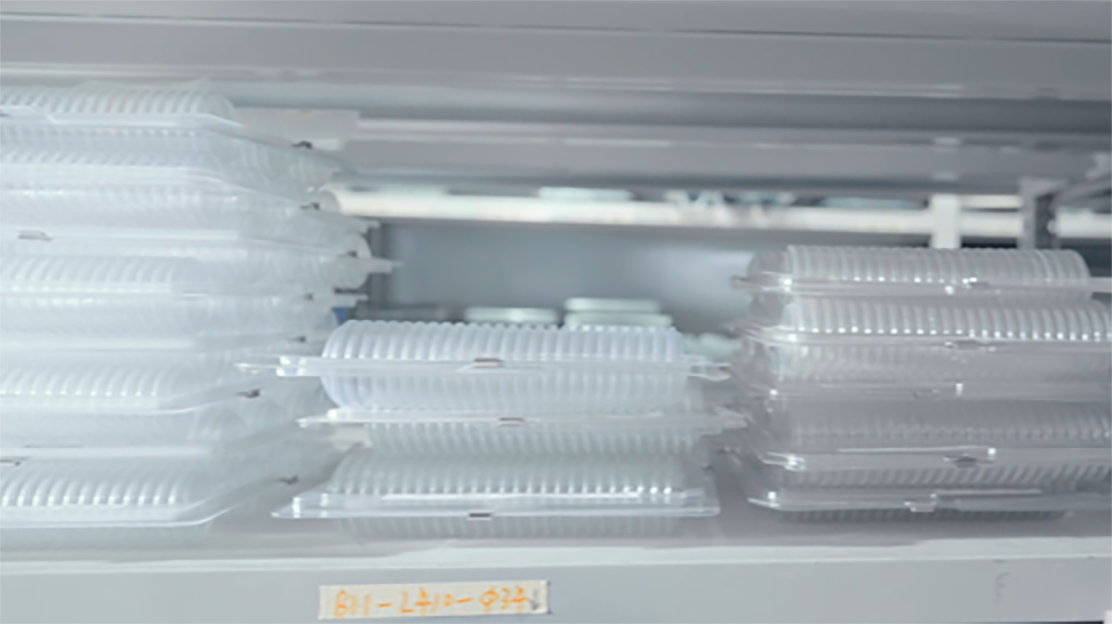
Packaging Standards
Our packaging complies with ISTA-certified transportation test protocols. All products are protected with scratch-resistant, anti-static, and impact-absorbing materials.

Protective Measures Include:
Vacuum-sealed bags for sensitive optics
Moisture-proof bags with desiccants
ESD-safe packaging for electronic components
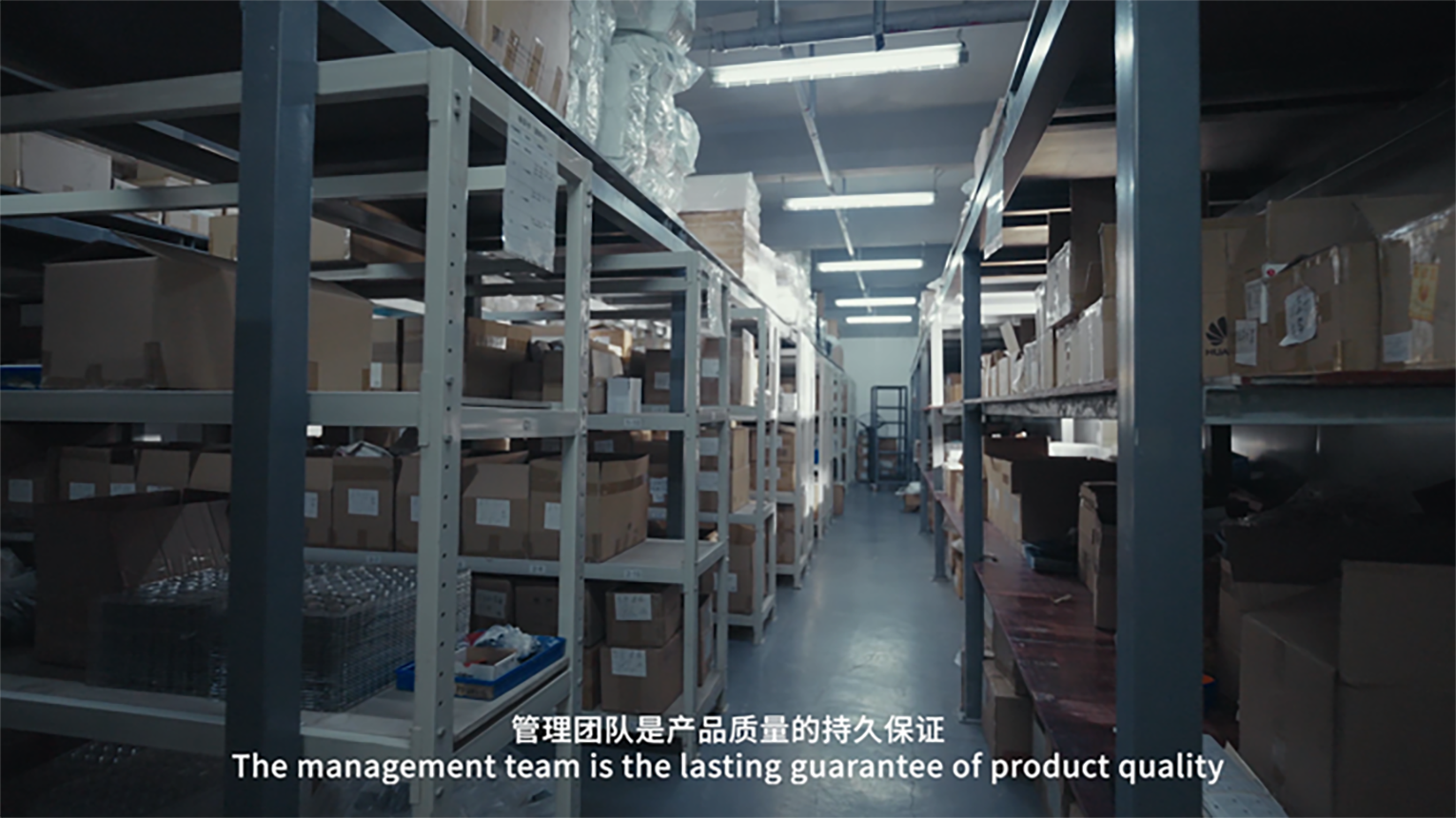
Container Loading Supervision
For bulk orders, we conduct container loading inspections to ensure optimal space utilization and secure handling.
Continuous Improvement & Customer Feedback
Quality is a Continuous Commitment
Corrective & Preventive Actions (CAPA)
We monitor quality metrics across all stages and implement data-driven improvements to reduce defects and enhance process stability.
Customer Feedback Loop
We value all customer feedback and maintain dedicated channels for issue reporting, suggestions, and product enhancement requests.
Quality Objectives
We aim to maintain a shipped defect rate below 300 PPM and continuously strive to exceed international optical standards.
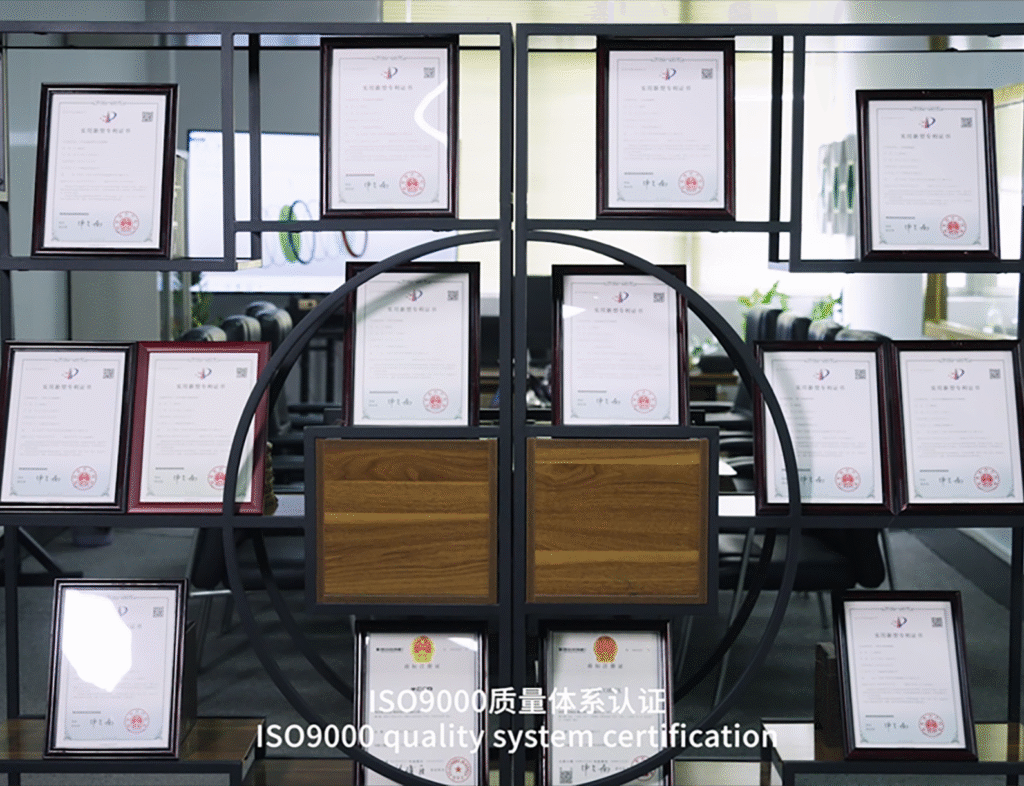
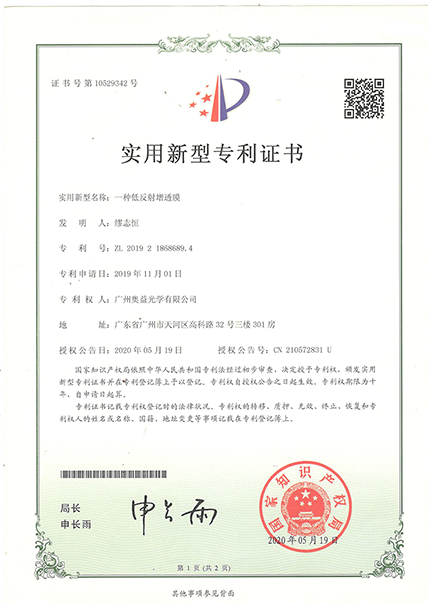
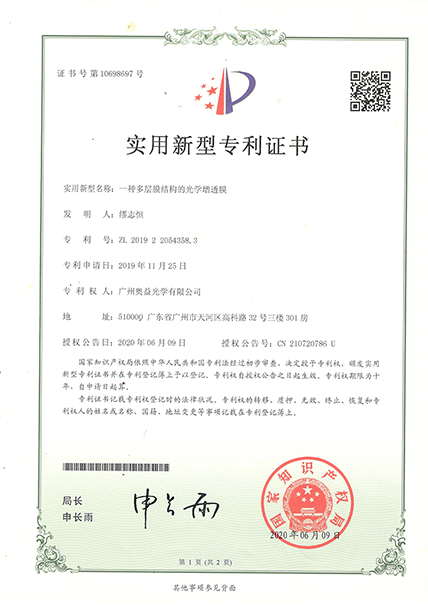

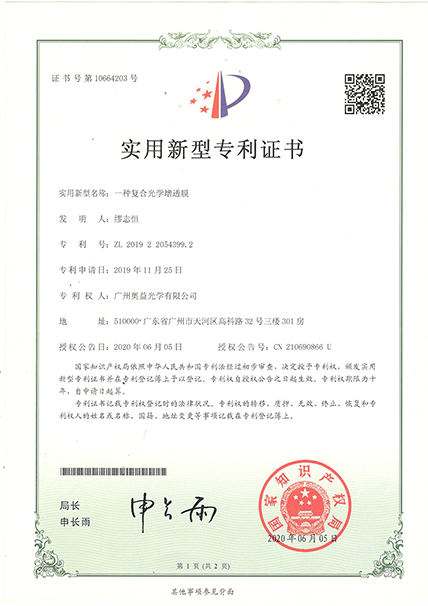

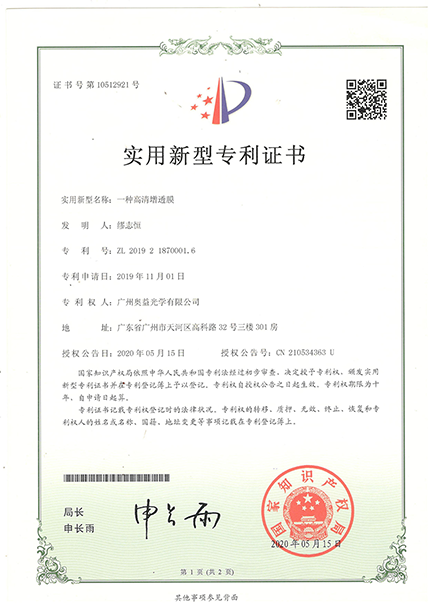
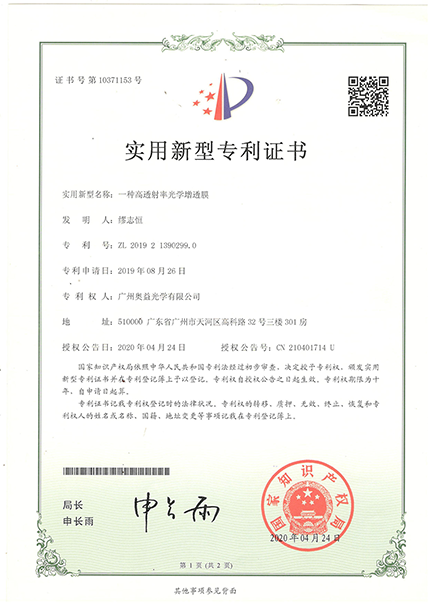
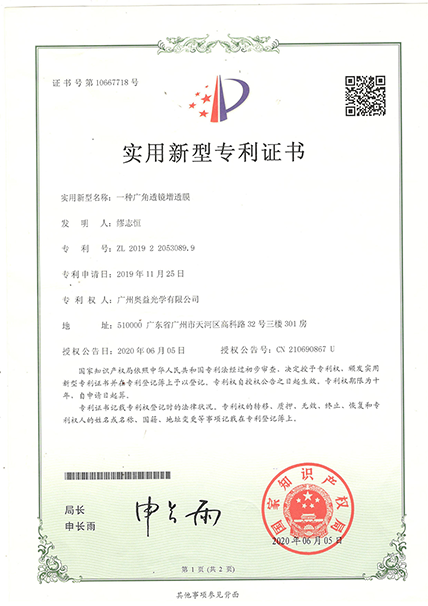
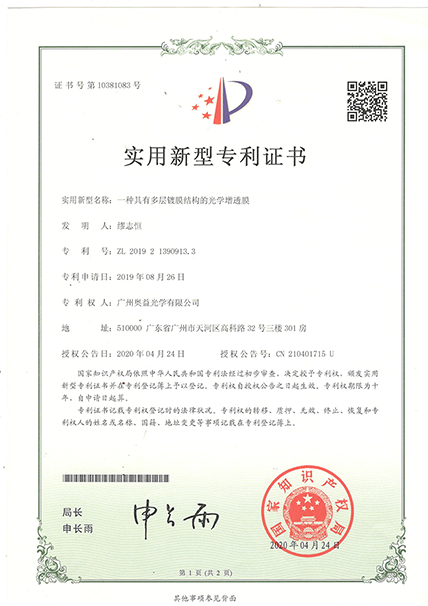

Connect with Our Quality Team
Expect More from Your Optical Components
Your challenge is our blueprint. Share your specifications and discover why MECO sets the benchmark in optical excellence.
Apply today for a free, customized optical solution.